
HubOne - Inbounding
Project overview
HubOne is the primary app used in Flink's warehouses, or "Hubs," to manage the daily inventory flow of products coming in and going out. With four key features—Activities, Inventory, Picking, and Inbounding—the app streamlines essential warehouse operations. The inbounding feature manages the receipt and storage of goods from Flink suppliers to warehouses daily. To enhance it, we focused on improving accuracy and speed, allowing warehouse operators to inbound products efficiently and allocate them on shelves faster—ensuring timely order preparation for riders.
I focused on three main aspects to achieve this goal.
-
Research how the current process of inbounding works, identify the possible reasons why there are inaccuracies when updating stock numbers and also why orders take too long to be prepared.
-
Ideate around new flow that can help to speed up and bring accuracy to the inbounding process and product shelf allocation.
-
Finalize designs for MVP, prototype and test.
Inbounding
Existing workflows
There are two inbounding flows for products: one for main suppliers—the primary flow—and another for smaller, regional suppliers.
To provide more context, deliveries arrive at the hubs in "Rolls"—mixed containers holding various items like milk, sugar, and toilet paper. Each Roll includes a QR code that details the products and quantities inside.
For main suppliers, a bulk inbounding process was used:
-
Scan the QR code on each Roll.
-
Once the product list loads, confirm the details.
-
Repeat for each Roll.
For other suppliers, inbounding required a manual process:
-
Scan each product individually.
-
Enter the quantity for each item.
-
Load as many products as needed.
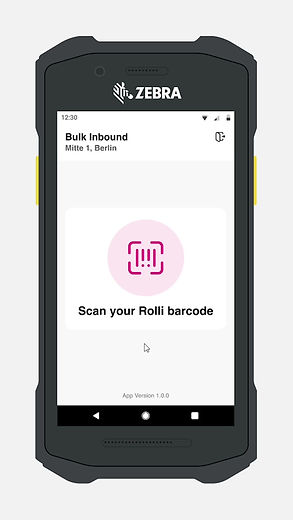
Research Plan
and conclusions


Our observations show that while the
"bulk inbounding" method efficiently makes products available online, it is inefficient for order preparation. Products are often left unpacked in rolls, requiring operators to spend excessive time locating items.

Time spend
One order took 32 minutes to prepare, with a single item search lasting 13 minutes—three times longer than the standard preparation time for large orders.

Limited verification
Few operators verify quantities due to a long, unsorted list of items, making manual checks slow and impractical.

Stock Inaccuracy Issues
Errors in stock numbers occur frequently, often due to prefilled incorrect numbers in the system.

Product Card Limitations
Product cards lack key details (e.g., origin and packaging type for produce), further complicating sorting and accurate inventory entry.
Hypothesis
We believe that by revamping the inbounding process—enabling operators to create customized product lists instead of using preloaded ones—will help reduce stock inaccuracies. This change will allow operators to verify the actual quantities, type, and origin of products arriving at the Hub. Additionally, by labeling a product as “Inbounded” only once it has been placed on the shelf, we will minimize “picking time” bottlenecks and accelerate the order preparation process.
Ideation
Flow and product cards UI
After defining the problem statement with the product team and defining design requirements, I splitted the explorations in two, flow discovery, and new product cards UI. Important to highlight there was also a design discovery of the complete app UI redesign and navigation, inbounding was the use cases that set the base for the general design of the app.
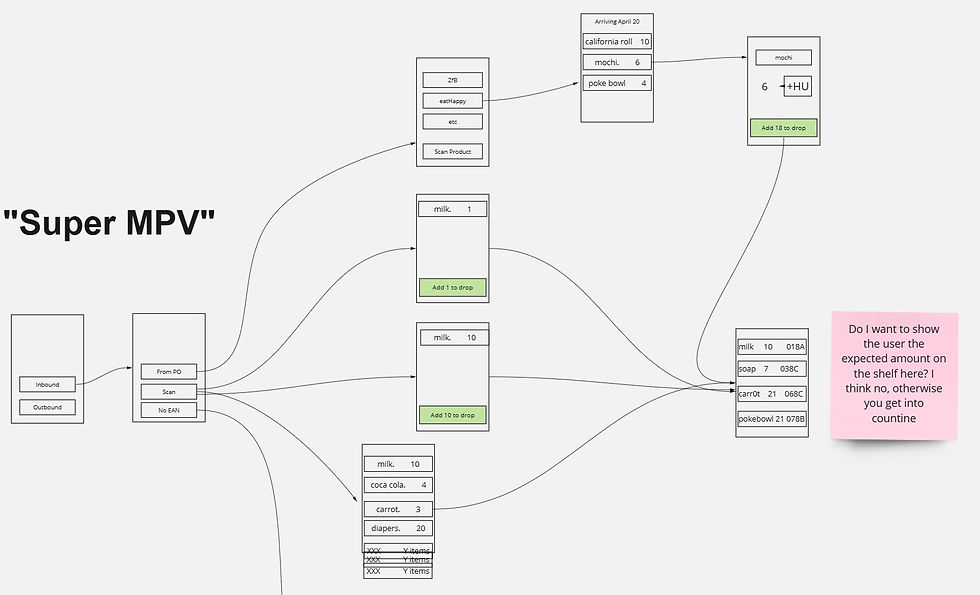
We began exploring ways to add products to a customized list and to differentiate between items that arrive in boxes versus single units.

We explored inbounding options like a "check-in" process focused solely on verifying product quantities upon arrival, followed by shelf allocation.
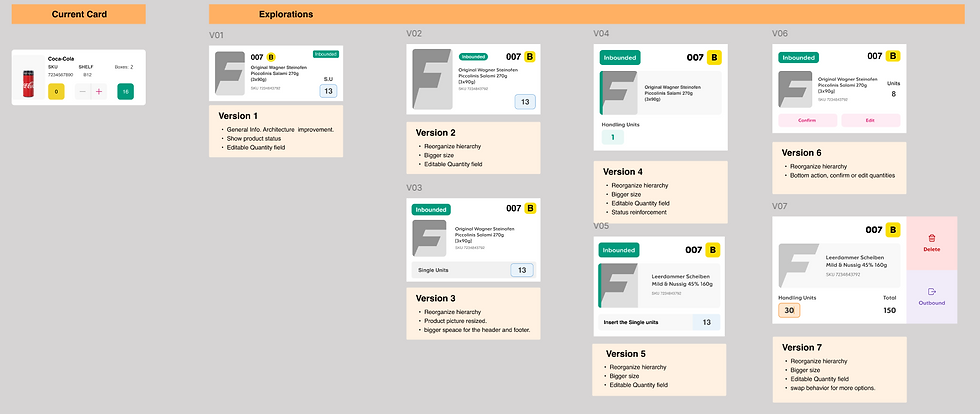
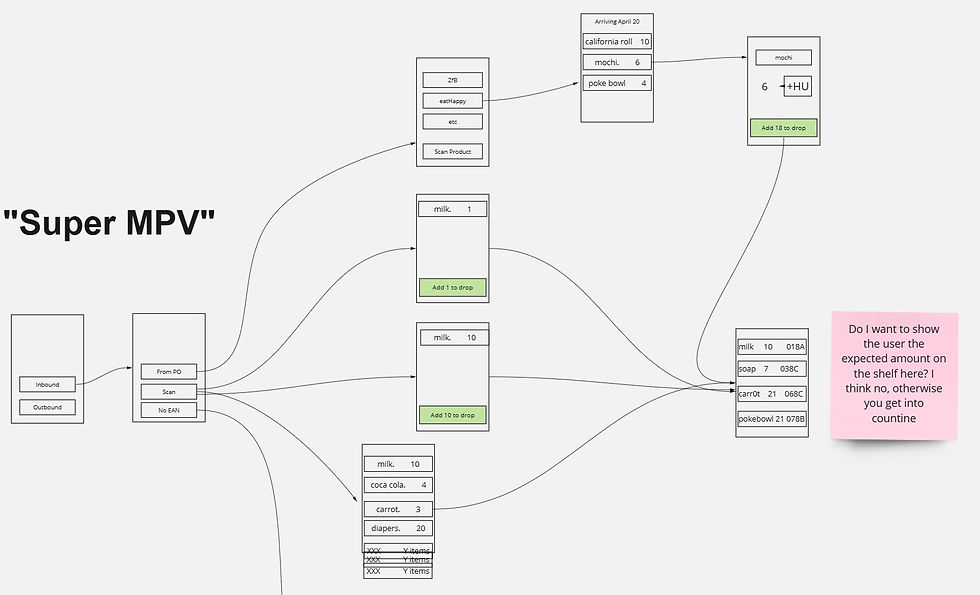
We began exploring ways to add products to a customized list and to differentiate between items that arrive in boxes versus single units.
Final Designs
Product cards
The selected version features a redesigned product card layout, offering enhanced visualization of product information, status, and quantity indicators. This improvement also provides clear guidance on how to allocate products on shelves and manage stock efficiently.
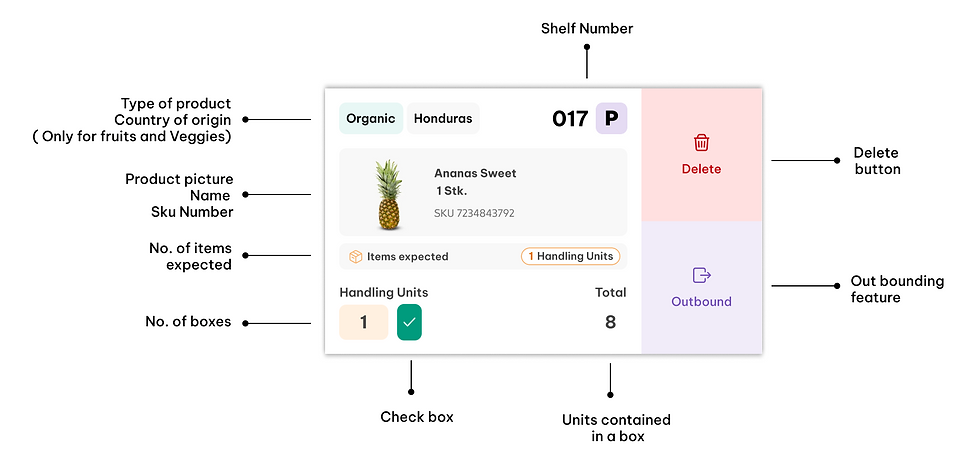

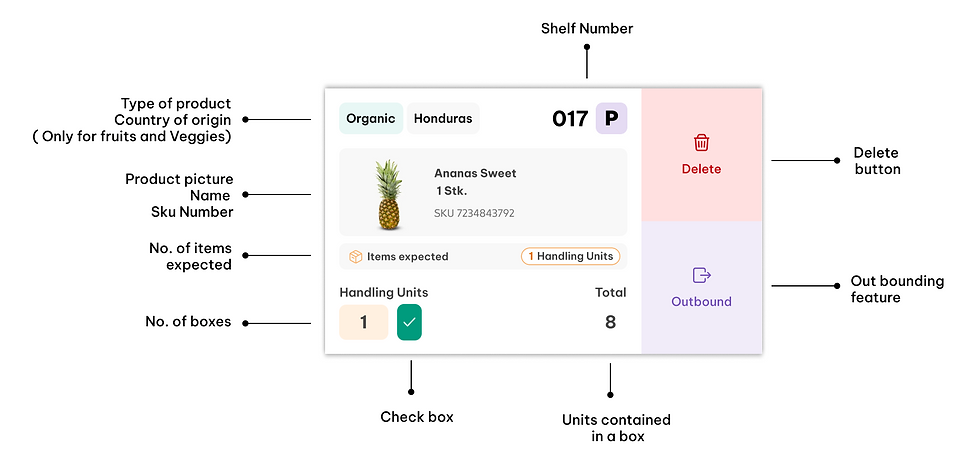
Inbounding Flow
The redesigned flow consists of three main steps: Supplier check-in, List preparation, and Dropping list. This streamlined process gives operators greater control over the products received at the hubs, enabling a more organized and efficient approach to stocking shelves. As a result, product shelves will remain consistently stocked and ready for pickers to prepare incoming orders seamlessly.
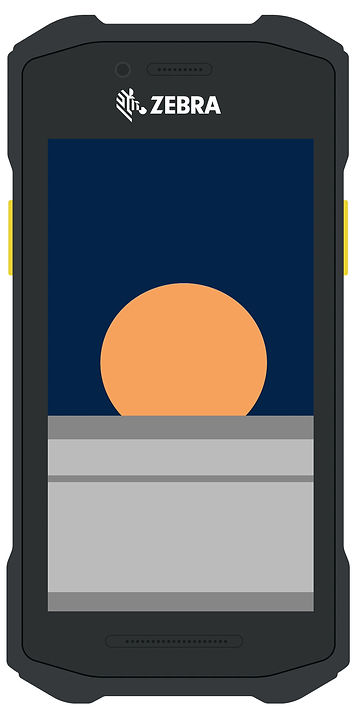
Step 1
Supplier CheckIn
This step introduces the user to the inbounding process, enabling the system to identify the supplier. It also generates events that facilitate more accurate data tracking.
Step 2
List preparation
This step involve creating a product list that will later be distributed across the hub, including shelves and backstock areas. The primary goal is to ensure control over the quantity and quality of the products received in the rolls.
To achieve this, the user simply needs to:
-
Add a product by scanning it or using the search bar.
-
Inspect the product to ensure it is in good condition.
-
Verify the received quantity by comparing the physical count with the pre-filled quantity
This process helps maintain accuracy and quality in inventory management.
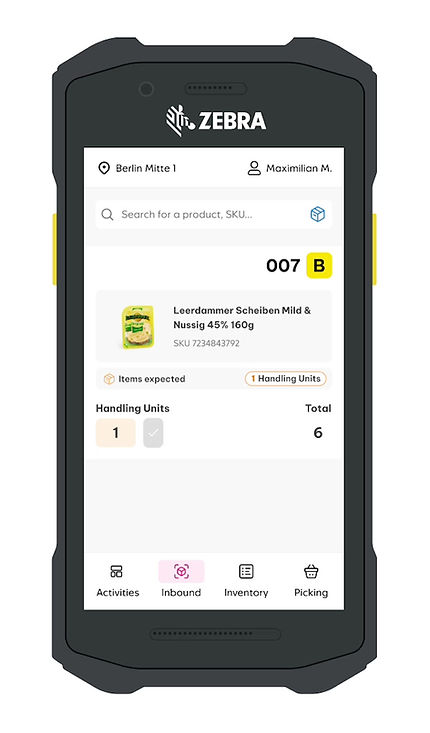

Step 3
Dropping List
After completing a product list with more than 10 items, the next step is to distribute the products across the hub
-
Sort the list in ascending or descending order based on the hub's shelf layout and the load station's North-to-South arrangement.
-
Find the designated shelf for each product.
-
Mark the product as inbounded by tapping its card in the list—only after placing it on the shelf.
After all items in the list are inbounded, the user can begin creating a new list.
Our Key Wins with the MVP

12 min saved
per order preparation
on average per large orders that contain more than 20 products.

15 % improvement
on stock accurancy
Hubs Increased their stock accuracy from 65% to 80%.

30 % increase
users satisfaction
"Since the new feature release, we've seen a 30% increase in active users, indicating positive reception and satisfaction."